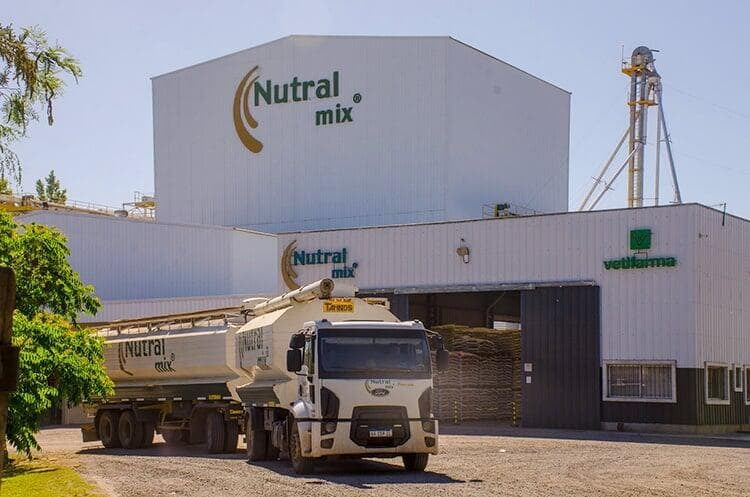
Mediante la implementación de las soluciones de productos y servicios de Powermeter la empresa Nutralmix pudo reducir sus costos energéticos en un 24%, además de mejorar su desempeño ambiental. Como resultado del proceso se encontraron importantes oportunidades para mejorar la contratación de energía, reemplazo de motores, revisión de fugas de aire comprimido, reparación de aislaciones del sistema de vapor y en el aprovechamiento de los sistemas fotovoltáicos.
En un mundo donde la eficiencia energética se ha convertido en un pilar fundamental para el sector industrial, Nutralmix, empresa argentina dedicada a la producción y comercialización de insumos para la nutrición y salud animal, enfrentó el desafío de reducir sus costos energéticos y en paralelo mejorar su impacto ambiental. Nutralmix se contactó con Powermeter con el objetivo de reducir el costo energético manteniendo los niveles de producción, mejorar su huella de carbono con acciones lo más costo-efectivas posibles y sentar las bases para implementar un sistema de gestión de energía en la nube. Para este proyecto se planteó una revisión de contratos energéticos, una auditoría energética y una campaña de medición integral en su planta de producción en 9 de Julio, provincia de Buenos Aires.
Metodología utilizada
La fase inicial del levantamiento de información y relevamiento se llevó a cabo en un trabajo coordinado con el equipo técnico de Nutralmix. Durante este proceso, se seleccionaron cuidadosamente los sitios para la instalación de los medidores Powermeter. Adicionalmente, se solicitó información inicial crucial para el diagnóstico energético, incluyendo facturas de energía, planos de sistemas de electricidad, aire comprimido, vapor, contratos de energía y planos o layouts de las instalaciones lo que sirvió para planificar la recorrida y los trabajos realizados en campo.
Una vez determinados los sectores a medir, se desplegaron 6 medidores inteligentes Powermeter para capturar datos de consumo en áreas y equipos clave; determinando los usos significativos de energía. Esta fase fue crucial para obtener una visión clara del uso energético en la planta y encontrar oportunidades y medidas de ahorro. El procesamiento de la información se realizó en la plataforma Powermate, que permite la gestión y análisis de gran cantidad de datos energéticos en una nube.
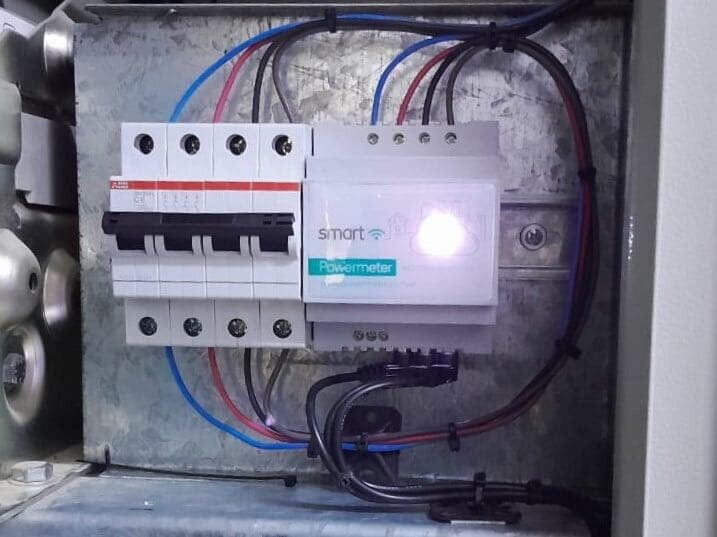
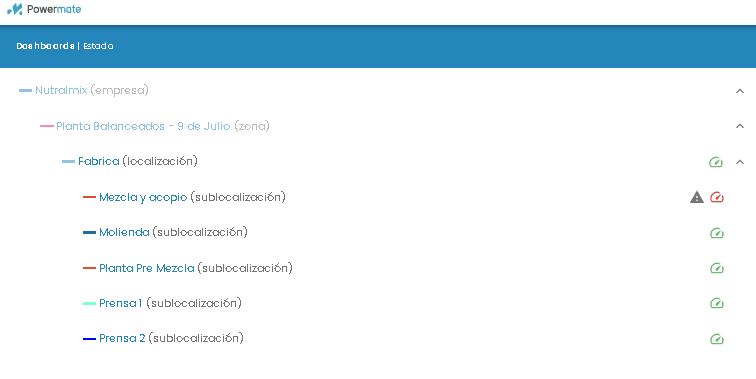
Una vez revisada la información inicial y analizados los datos de una semana completa de medición se realizaron las visitas de la auditoría de energía. Las mismas fueron realizadas por uno de nuestros partners técnicos especialistas en eficiencia energética y llevaron una jornada de un día en donde se relevaron todos los equipos/sistemas y se realizaron mediciones puntuales e instantáneas (termográficas, mediciones instantáneas de corriente y de fugas de aire comprimido).
Los resultados de la auditoría fueron compilados en un informe final, con el resultado que permitía priorizar las oportunidades de ahorro y las recomendaciones para mejorar la eficiencia energética. Estos resultados fueron presentados de manera virtual a la dirección y gerencia de Nutralmix, los que sirvieron como base para la elaboración de un plan de acción y determinar las decisiones estratégicas para la gestión energética.
Contratación de energía
Se realizó una revisión general de las facturas y contratos de energía eléctrica, de gas natural y de energía renovable. Se identificaron oportunidades de ahorro de un 15% (electricidad y gas natural) y entregó un informe de contratación de energía con las recomendaciones y pasos a seguir. Las mejoras encontradas fueron:
Revisar el proceso de licitación de contratos de gas
Optimizar el contrato de electricidad con la cooperativa
Mejorar el contrato de energía solar con la cooperativa
Análisis de las mediciones
La campaña de medición consistió en instalar 1 medidor a nivel general y otros 5 en los tableros secundarios de mayor potencia. La medición a lo largo del tiempo permitió priorizar los usos significativos de la energía. Asimismo se coordinaron una serie de operaciones con el área de producción y mantenimiento para determinar la operación y control de ciertos equipos. Un ejemplo de esto fue la medición puntual del consumo del sistema de aire comprimido, coordinado con una parada de planta de 3hs para determinar el consumo y el costo total de las fugas de aire comprimido.
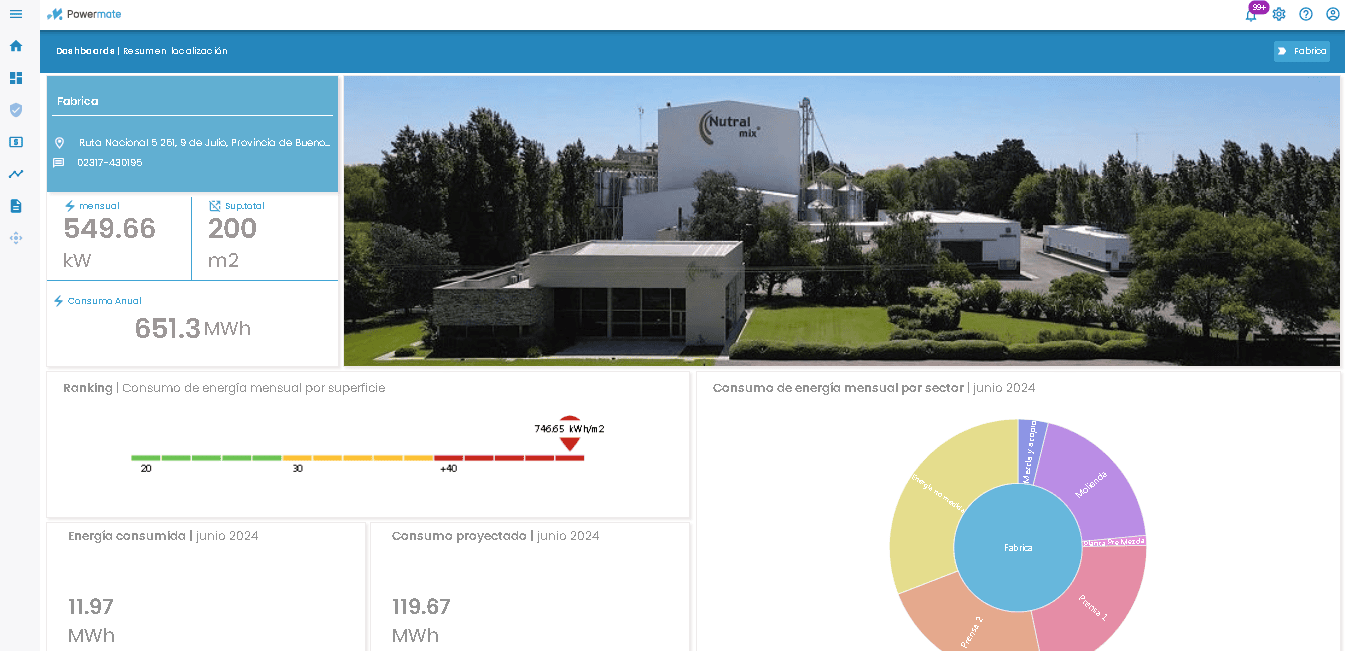
Auditoría de energía
Con la intervención de partners técnicos de Powermate se implementó una auditoría energética en donde se relevaron todos los sistemas, equipos e instalaciones. Se realizaron mediciones puntuales e instantáneas utilizando equipos como luxómetros, cámaras termográficas, equipos por ultrasonido y pinzas amperométricas. Luego se complementó y se cruzaron los datos relevados en la auditoría de energía con la campaña de medición. Estos trabajos permitieron encontrar mejoras en el orden de un 15% en los siguientes sistemas:
Motores
Iluminación
Aire comprimido
Vapor
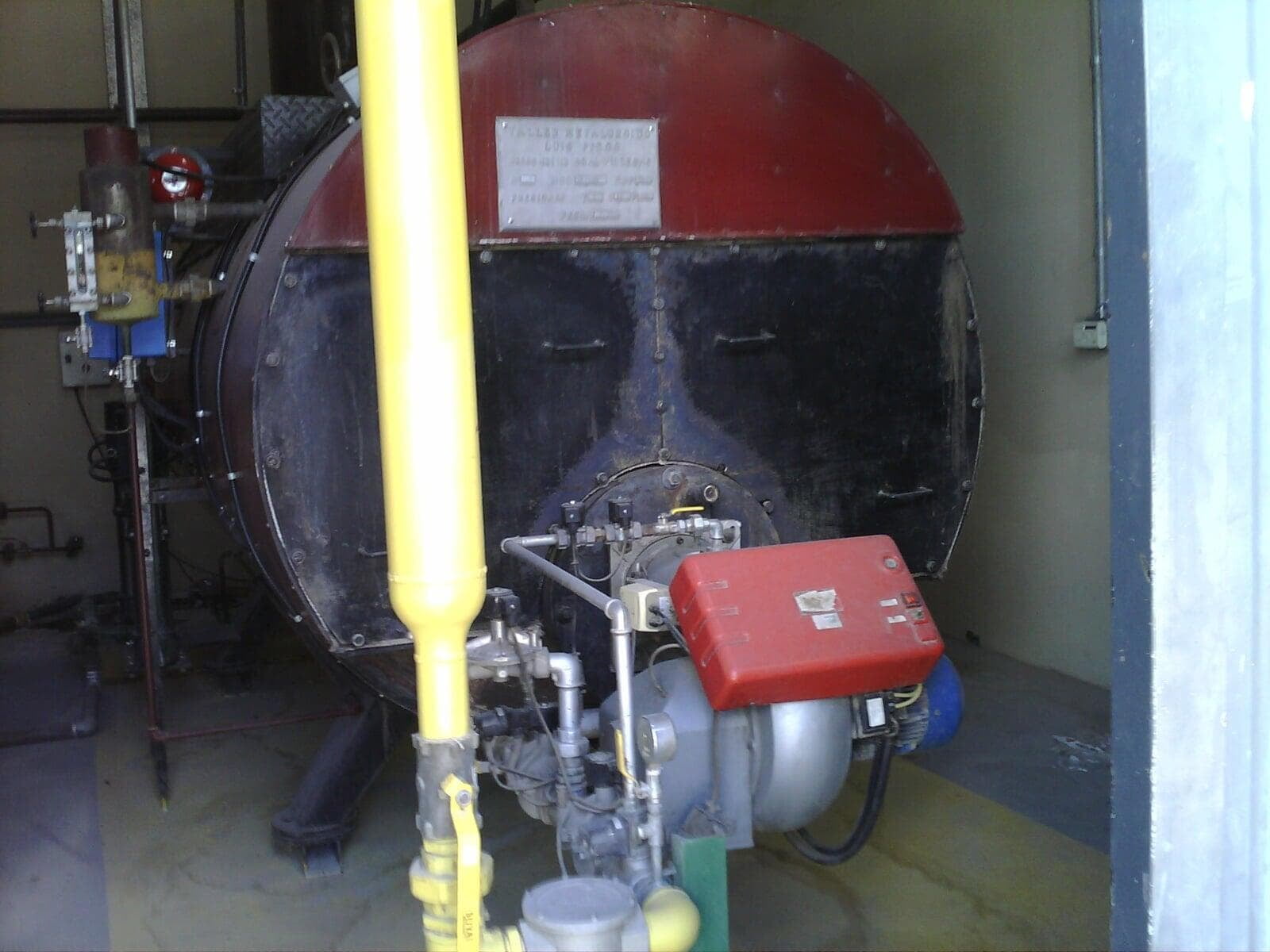
Figura: Caldera de vapor
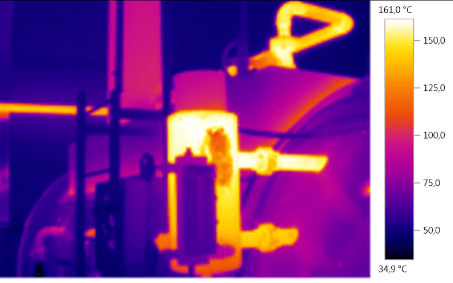
Colector de vapor

Powermeter instalado
Calidad de Energía
Durante la visita a la planta se realizó un análisis de la calidad de la energía, llevando a cabo mediciones y visualizaciones. Mediante los medidores Powermeter instalados se pudo profundizar en aspectos como cortes eléctricos, variaciones en los valores de tensión y desequilibrios entre las fases. Esta evaluación permitió asegurar el correcto funcionamiento de la instalación, además de identificar áreas de mejora para mejorar la eficiencia energética de la planta.
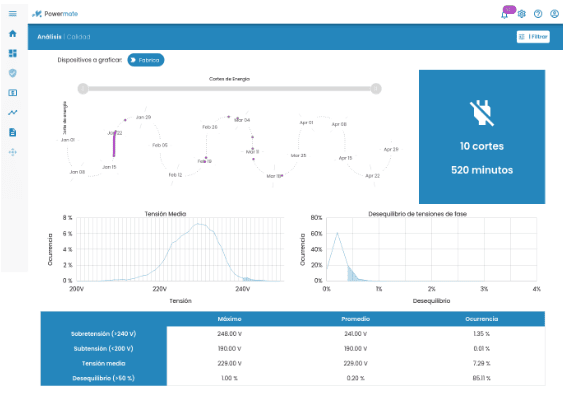
Análisis mediante HeatMap
En la plataforma Powermate utilizamos la herramienta "Heatmap" que nos facilitó identificar de manera rápida y eficaz cualquier desvío en los patrones de consumo de energía. Esta herramienta permite analizar de una forma gráfica los usos de la demanda de potencia y energía por horarios e identificar fácilmente patrones de consumo. En este caso se pudo comprobar que no hay consumos significativos fuera de los horarios de operación, pero es importante controlar la constancia en el buen comportamiento de usos energéticos para no incurrir en gastos innecesarios.
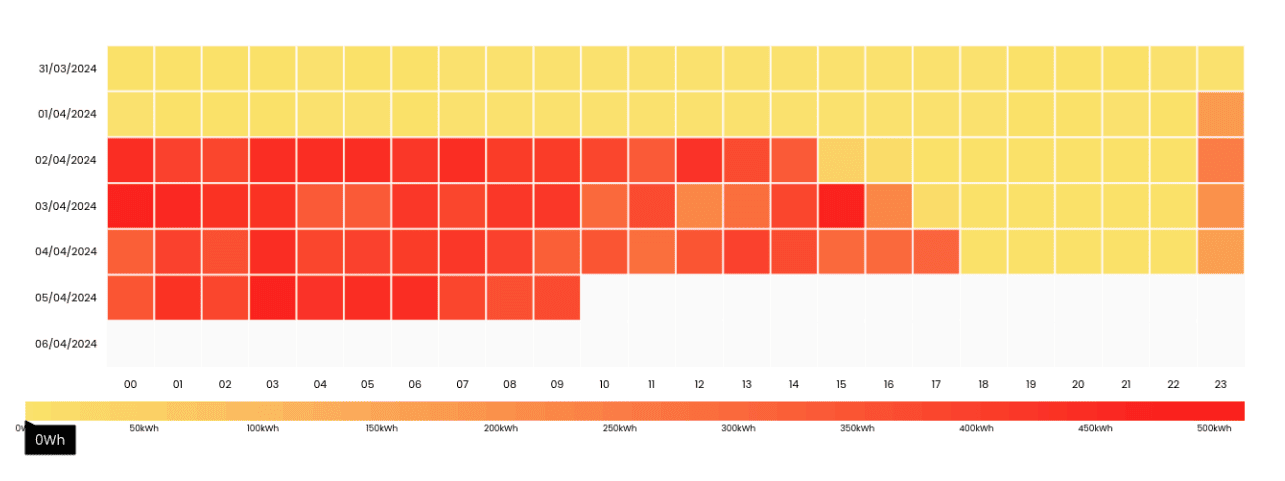
Aire comprimido
La revisión periódica de los circuitos es fundamental para evitar que se descontrolen los costos. En toda industria es inevitable tener un porcentaje de fugas porque se producen nuevas roturas continuamente. Pero este porcentaje no debiera exceder el 25 a 30% del caudal total. Durante el período de estudio se determinó que las fugas rondan el 60% del consumo total en aire comprimido. En la imagen que sigue se puede ver el consumo del compresor en momentos en que la planta estaba parada. Este consumo corresponde mayormente a la energía requerida para alimentar las fugas. Esto no sólo permitió identificar el problema sino cuantificar el impacto que tendrán los trabajos de reparación en las líneas de aire comprimido.
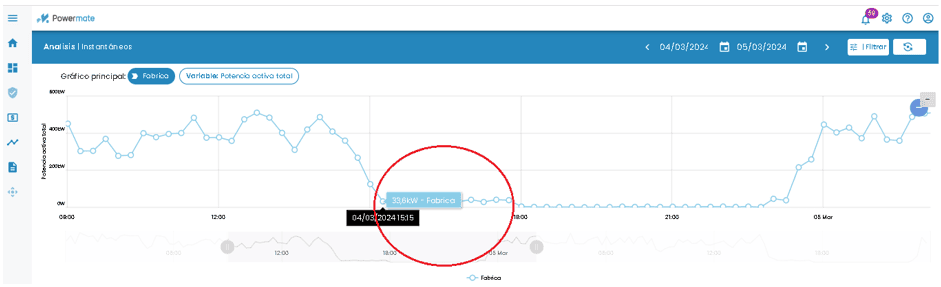
Dashboard operativo personalizado
Se generó un tablero de control (dashboard) en la plataforma Powermate para facilitar el monitoreo en tiempo real. En él se reúnen las mediciones de potencia activa de los 6 medidores utilizados en la campaña de medición, además del consumo de energía diario de la planta durante el mes en curso. De esta forma se puede tener una idea del comportamiento energético rápidamente y de fácil entendimiento.
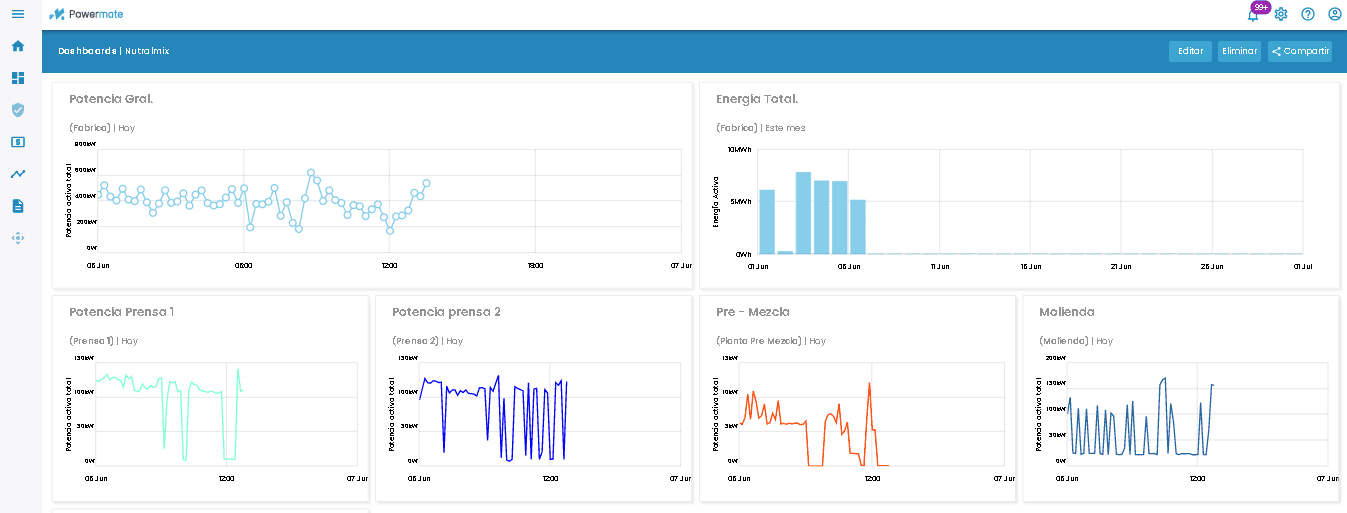
Resultados
Se identificaron ahorros económicos en torno a un 24% del total de energía consumida (electricidad y gas natural). A continuación se realiza un detalle de las oportunidades y ahorros encontrados :
Contratación de energía: Se detectaron posibilidades de mejorar un 15% los costos de los contratos energéticos.
Gestión de motores: Se propusieron políticas para la gestión, mantenimiento y recambio por motores de alta eficiencia, lo que resulta en una reducción estimada del 2% en el consumo de energía anual.
Aire comprimido: Se identificaron, cuantificaron, priorizaron y repararon fugas de aire comprimido; y se establecieron rutinas de control operacional para mejorar la utilización de los sistemas lo que permite reducir el costo de energía eléctrica en un 5%.
Generación de vapor: se identificaron aislaciones deficientes del sistema de vapor y posibilidades de optimizar la combustión lo que reduce el consumo de gas natural en la caldera en un 2%.
Este caso de éxito demuestra que es posible reducir los costos energéticos en el sector industrial realizando proyectos de nula o baja inversión como análisis de contratación de energía, campañas de medición o diagnósticos energéticos llegando a resultados de hasta un 24% menos comparados con la situación inicial.
"La colaboración con Powermeter nos ha permitido revisar y mejorar los contratos de energía, encontrar cuales son nuestros consumos más importantes y trazar un plan de acción de eficiencia energética. Tenemos por delante llevar este plan con el objetivo de reducir nuestro costo de energía un 24%"